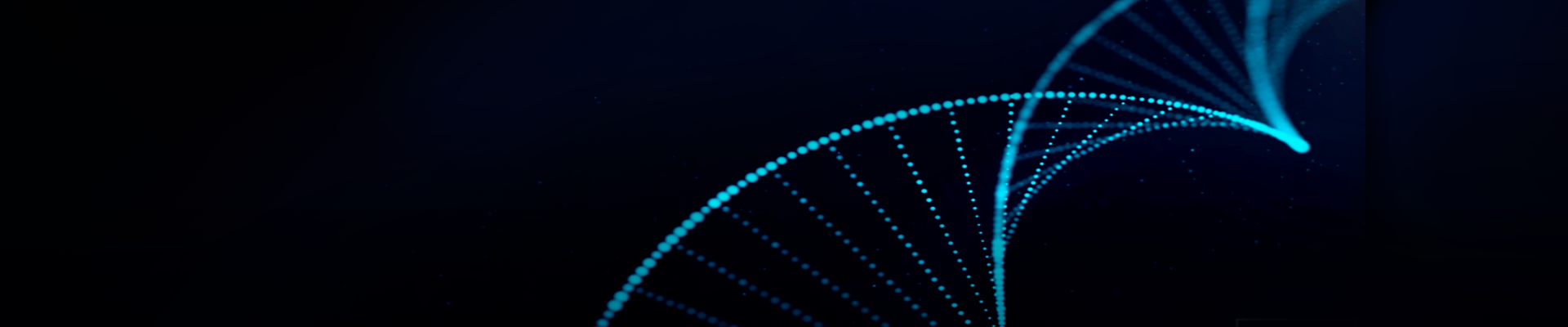
Case Studies
INSTILLING A LEAN PHILOSOPHY
The Challenge
Bouncing back from an industry recession, MCRD Manufacturing, a mid-size home furnishings manufacturer, faced an exciting challenge: meet increased demand, improve quality, and reduce costs. In response to Corporate’s encouragement for the Plant Manager to address this problem as he saw fit, he decided to implement a Lean manufacturing process to meet these goals.
Lean’s approach and proven results would increase the plant’s capacity, reduce costs, and minimize the need for seasonal help. The Plant Manager knew that Lean required a significant shift from a top-down-driven, only-management-makes-critical-production-decisions culture, to a flatter, more inclusive and participatory one. Having led this type of change in his former company he knew that culture change was a difficult but achievable goal.
He engaged a Lean consultant to guide the change by training the staff in Lean and advising him on best ways to manage the required culture change. The Lean consultant recommended that the Plant Manager assess the culture to identify the roadblocks and measure progress. He recommended Strategia Analytics’ DnA® assessment.
The Results showed that the team members had high trust in their managers and a strong affinity for and loyalty toward the organization.
They also showed a strong bias toward being experimental in their approach to solving problems and a willingness to find non-standard ways to make things work, backed by an innovative HR approach.
After review of the assessment results, all management team members supported the decision to adopt a Lean philosophy. To begin the transformation, the Plant Manager personally communicated the ideas and rationale for change to all employees and asked for their help, while promising to provide the training needed and to share the benefits of the change.
The Solution
The Plant Manager dedicated resources to teaching Lean principles to the entire workforce while enhancing the supervisory skills of his leadership team. Training was not once and done; new hires were trained as they came in. Everyone was rotated through both classroom and hands-on training at least annually.
Continuous Improvement Teams were created, each initially led by a management team member, followed by more leaders being recruited from the workforce and given extra training. Temporary employees were trained in the principles as they joined the company.
The mantra for all became Safety=Quality=Productivity.
The Results
The company’s “Mod Rate,” the multiplier applied to Workers Comp insurance, dropped steadily over a 7-year periods from 1.80 to 0.77.
Quality improved. Over a 6-year period the value of product returned due to manufacturing errors dropped from $20,800 to $11,700—a reduction of 44% without even accounting for price and volume increases.
The very first production line adopting a Lean approach showed an increase of 40% within three weeks, from 20 product assemblies per hour with 6 people to 27.5 assemblies per hour with 5 people.
Most importantly, the factory added five production lines within its original footprint to produce the new product lines the company introduced.
Over time, the other plants, that had not gone Lean, became significantly less profitable and were closed; all manufacturing for the corporation moved to this location.
The Plant Manager put a succession plan in place to continue to grow the talent of future in-house leaders.
Subassemblies are now made-to-order in-house without additional people; all operators involved in this process were freed up by making existing lines Lean. Now, instead of being purchased based on a forecast, these items are made on-site as needed, saving inventory dollars, warehouse space, and in-bound transportation costs.
Lessons Learned
Empowering employees and developing managerial skills enhances a culture of respect and cooperation. As attitudes change, behaviors change, a key factor in the improvements noted above.
As enthusiasm and engagement build, the normal pace of operations picks up. People learn to take responsibility for their own work areas and output; they join cross-functional teams to solve problems, remove delays, and reduce wasted effort.
Supervisors learn to become team leaders and quality assurance inspectors become active problem-solving team members. Most importantly, team members thrive in the changed culture—willingly showing new employees and the influx of seasonal employees the new norms of how the team takes care of THEIR line and handles THEIR product.
Operational DnA® Assessment results over a 5-year period showed a significant increase in employee empowerment, supervisory and employee engagement, and understanding of the plant’s and the company’s strategy.
Subsequent Steps
Survey results of the management team’s future goals showed a desire to see even greater employee development and empowerment
The change in culture that allowed this is quantifiable. People reported a very high understanding of their expectations and the company’s purpose. Accountability, responsibility and teamwork broadened considerably from the first survey.
Increasing inclusion and empowering employees enhanced a culture of respect and cooperation.
As attitudes changed, behaviors changed, multiplying the impact of Lean. This new culture was sustained through Strategia’s last measurement seven years after Lean was initiated.
The manufacturer’s next concern was the impact on their Lean culture of a forecasted rapid increase in the workforce, and the plant manager again asked us for guidance. We helped them see how the strengths they built would be the basis for continued success.